Погана водостійкість, нерівна поверхня, високий вміст порошку та нерівномірна довжина? Поширені проблеми та заходи щодо покращення у виробництві кормів для водних організмів
У нашому щоденному виробництві кормів для водних тварин ми стикалися з деякими проблемами з різних аспектів. Ось кілька прикладів для обговорення з усіма:
1. Формула
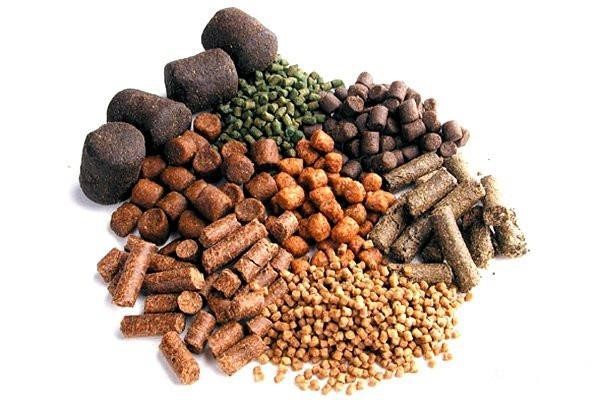
1. У формулі корму для риб є більше видів сировини для шроту, такої як ріпаковий шрот, бавовняний шрот тощо, які належать до сирої клітковини. Деякі олійні заводи використовують передові технології, і олія в основному обсмажується насухо з дуже низьким вмістом. Крім того, ці види сировини погано засвоюються під час виробництва, що значно впливає на грануляцію. Крім того, бавовняний шрот важко подрібнити, що впливає на ефективність.
2. Рішення: Збільшено використання ріпакової макухи, а також додано високоякісні місцеві інгредієнти, такі як рисові висівки. Крім того, додано пшеницю, яка становить приблизно 5-8% формули. Завдяки коригуванню ефект грануляції у 2009 році є відносно ідеальним, а вихід на тонну також збільшився. Частинки розміром 2,5 мм становлять від 8 до 9 тонн, що майже на 2 тонни більше порівняно з минулим роком. Зовнішній вигляд частинок також значно покращився.
Крім того, щоб покращити ефективність подрібнення бавовняного шроту, ми змішали бавовняний та ріпаковий шрот у співвідношенні 2:1 перед подрібненням. Після покращення швидкість подрібнення була практично на рівні швидкості подрібнення ріпакового шроту.
2. Нерівна поверхня частинок
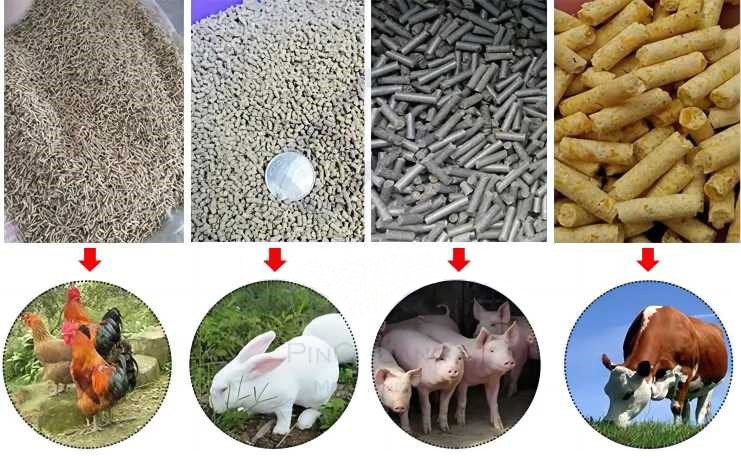
1. Він має великий вплив на зовнішній вигляд готового продукту, а при додаванні до води схильний до руйнування та має низький коефіцієнт використання. Основна причина полягає в наступному:
(1) Сировина подрібнюється занадто грубо, і під час процесу відпуску вона не повністю дозріває та розм'якшується, і не може добре поєднуватися з іншою сировиною під час проходження через отвори форми.
(2) У кормовій суміші для риби з високим вмістом сирої клітковини, через наявність бульбашок пари в сировині під час процесу темперування, ці бульбашки розриваються через різницю тиску між внутрішньою та зовнішньою частинами форми під час стиснення частинок, що призводить до нерівномірної поверхні частинок.
2. Заходи щодо поводження:
(1) Правильно контролюйте процес дроблення
Наразі, під час виробництва кормів для риб наша компанія використовує мікропорошок сита 1,2 мм як сипучу сировину. Ми контролюємо частоту використання сита та ступінь зносу молота, щоб забезпечити дрібність подрібнення.
(2) Контроль тиску пари
Відповідно до формули, під час виробництва слід розумно регулювати тиск пари, зазвичай контролюючи його приблизно на рівні 0,2. Через велику кількість грубоволокнистої сировини у формулі корму для риби потрібна високоякісна пара та розумний час темперування.
3. Погана водостійкість частинок
1. Цей тип проблеми є найпоширенішим у нашому щоденному виробництві та зазвичай пов'язаний з такими факторами:
(1) Короткий час темперування та низька температура темперування призводять до нерівномірного або недостатнього темперування, низького ступеня дозрівання та недостатньої вологості.
(2) Недостатня кількість клейких матеріалів, таких як крохмаль.
(3) Коефіцієнт стиснення кільцевої форми занадто низький.
(4) Вміст олії та частка сирої клітковини у формулі занадто високі.
(5) Коефіцієнт розміру частинок під час дроблення.
2. Заходи щодо поводження:
(1) Покращте якість пари, відрегулюйте кут лопаті регулятора, подовжте час темперування та відповідно збільште вміст вологи в сировині.
(2) Відрегулювати формулу, відповідно збільшити кількість крохмальної сировини та зменшити частку жиру та сирої клітковини.
(3) За потреби додайте клей. (Бентонітова суспензія на основі натрію)
(4) Покращити коефіцієнт стисненнякільцеподібна матриця
(5) Добре контролюйте тонкість подрібнення
4. Надмірний вміст порошку в частинках
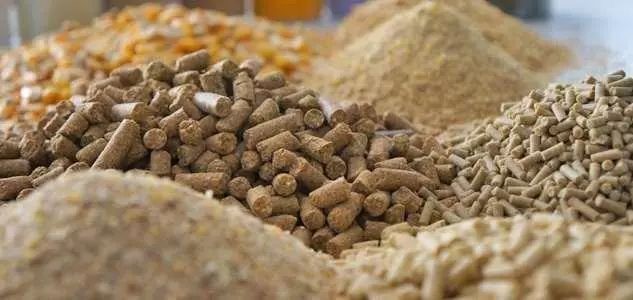
1. Важко забезпечити появу загальної гранульованої сировини після охолодження та перед просіюванням. Клієнти повідомляли, що в гранулах більше дрібної золи та порошку. Виходячи з вищезазначеного аналізу, я вважаю, що для цього є кілька причин:
A. Поверхня частинок не гладка, розріз не акуратний, а частинки пухкі та схильні до утворення порошку;
B. Неповне просіювання за допомогою сітки для сортування, засмічення сітки, сильний знос гумових кульок, невідповідність отворів сітки тощо;
C. На складі готової продукції багато дрібного зольного залишку, і очищення не є ретельним;
D. Існують приховані небезпеки у видаленні пилу під час пакування та зважування;
Заходи щодо поводження:
A. Оптимізуйте структуру формули, обґрунтовано виберіть кільцеву матрицю та добре контролюйте коефіцієнт стиснення.
B. Під час процесу грануляції контролюйте час темперування, кількість подачі та температуру грануляції, щоб повністю дозріти та пом'якшити сировину.
C. Переконайтеся, що поперечний переріз частинок акуратний, і використовуйте м’який ріжучий ніж, виготовлений зі сталевої стрічки.
D. Налаштуйте та підтримуйте екран оцінювання, використовуйте розумну конфігурацію екрана.
E. Використання технології вторинного грохочення на складі готової продукції може значно зменшити співвідношення вмісту порошку.
F. Необхідно своєчасно очищати склад готової продукції та контур. Крім того, необхідно покращити пристрій для пакування та видалення пилу. Найкраще використовувати негативний тиск для видалення пилу, що є більш ідеальним варіантом. Особливо під час процесу пакування працівник пакування повинен регулярно вибивати та очищати від пилу буферний бункер ваг для пакування..
5. Довжина частинок варіюється
1. У щоденному виробництві ми часто стикаємося з труднощами в управлінні, особливо для моделей понад 420. Причини цього приблизно підсумовані наступним чином:
(1) Кількість подачі для грануляції нерівномірна, а ефект темперування сильно коливається.
(2) Нерівномірний зазор між роликами форми або сильний знос кільцевої форми та притискних роликів.
(3) Уздовж осьового напрямку кільцевої форми швидкість вивантаження на обох кінцях нижча, ніж посередині.
(4) Отвір для зниження тиску кільцевої форми занадто великий, а швидкість відкриття занадто висока.
(5) Положення та кут ріжучого леза є неприйнятними.
(6) Температура грануляції.
(7) Тип та ефективна висота (ширина леза, ширина) леза для кільцевого висікання мають вплив.
(8) Водночас розподіл сировини всередині камери стиснення нерівномірний.
2. Якість кормів та гранул зазвичай аналізується на основі їхніх внутрішніх та зовнішніх якостей. Як виробнича система, ми більше схильні до факторів, пов'язаних із зовнішньою якістю кормових гранул. З точки зору виробництва, фактори, що впливають на якість гранул водного корму, можна приблизно підсумувати наступним чином:
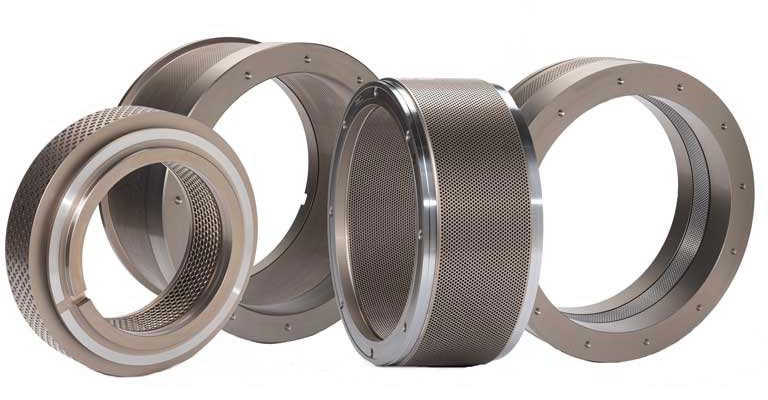
(1) Розробка та організація формул безпосередньо впливають на якість гранул водного корму, складаючи приблизно 40% від загальної кількості;
(2) Інтенсивність дроблення та однорідність розміру частинок;
(3) Діаметр, коефіцієнт стиснення та лінійна швидкість кільцевої форми впливають на довжину та діаметр частинок;
(4) Коефіцієнт стиснення, лінійна швидкість, ефект гартування та відпуску кільцевої форми, а також вплив ріжучого леза на довжину частинок;
(5) Вміст вологи в сировині, ефект темперування, охолодження та сушіння впливають на вміст вологи та зовнішній вигляд готової продукції;
(6) Саме обладнання, технологічні фактори, а також ефекти гартування та відпуску впливають на вміст частинок порошку;
3. Заходи щодо поводження:
(1) Відрегулюйте довжину, ширину та кут скребка для тканини та замініть зношений скребок.
(2) Звертайте увагу на своєчасне регулювання положення ріжучого леза на початку та ближче до кінця виробництва через невелику кількість подачі.
(3) Під час виробничого процесу забезпечте стабільну швидкість подачі та подачу пари. Якщо тиск пари низький і температура не може підвищитися, його слід своєчасно відрегулювати або зупинити.
(4) Розумно відрегулюйте зазор міжроликова оболонкаПісля встановлення нової форми встановіть нові ролики та своєчасно відремонтуйте нерівну поверхню притискного ролика та кільцевої форми через знос.
(5) Відремонтуйте напрямний отвір кільцевої форми та негайно очистіть засмічений отвір форми.
(6) Під час замовлення кільцевої форми коефіцієнт стиснення трьох рядів отворів на обох кінцях осьового напрямку оригінальної кільцевої форми може бути на 1-2 мм меншим, ніж посередині.
(7) Використовуйте м’який ріжучий ніж товщиною від 0,5 до 1 мм, щоб забезпечити максимально гостру кромку, яка знаходиться на лінії зчеплення між кільцевою формою та притискним роликом.
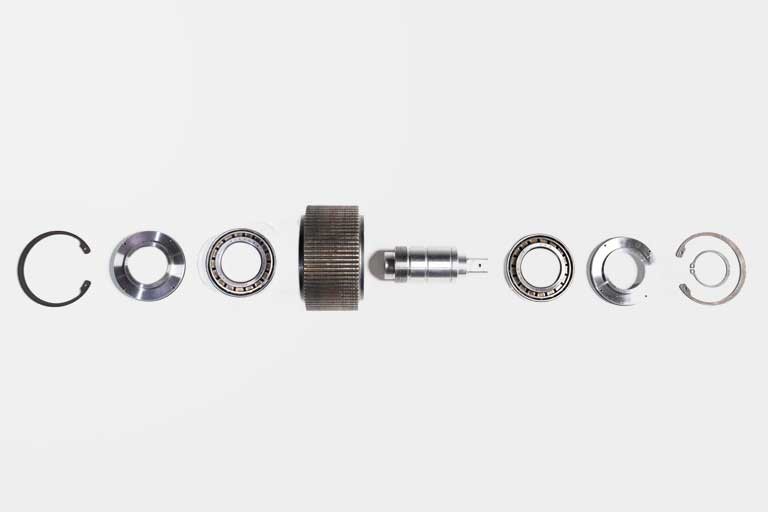
(8) Забезпечте концентричність кільцевої форми, регулярно перевіряйте зазор шпинделя гранулятора та за потреби відрегулюйте його.
6. Контрольні точки:
1. Подрібнення: Тонкість подрібнення повинна контролюватися відповідно до вимог специфікації
2. Змішування: Рівномірність змішування сировини необхідно контролювати, щоб забезпечити відповідну кількість змішування, час змішування, вміст вологи та температуру.
3. Дозрівання: Тиск, температура та вологість у машині для надування повинні контролюватися
Розмір і форма частинок матеріалу: необхідно вибрати відповідні характеристики прес-форм та ріжучих лез.
5. Вміст води в готовому кормі: Необхідно забезпечити час і температуру сушіння та охолодження.
6. Розпилення олії: Необхідно контролювати точну кількість розпилення олії, кількість форсунок та якість олії.
7. Просіювання: Виберіть розмір сита відповідно до характеристик матеріалу.
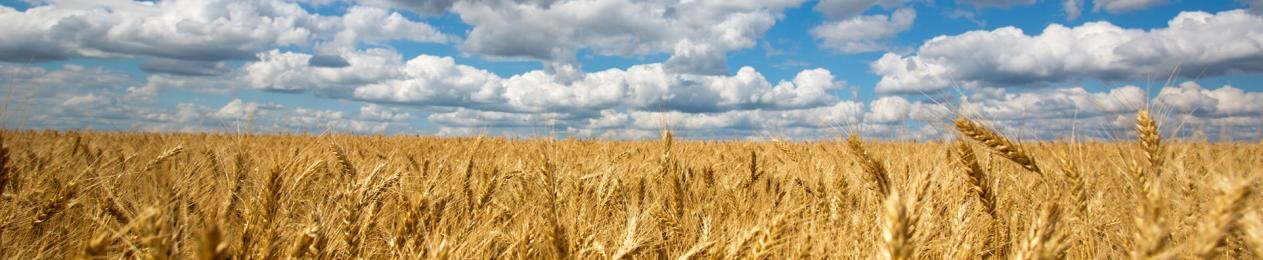
Час публікації: 30 листопада 2023 р.